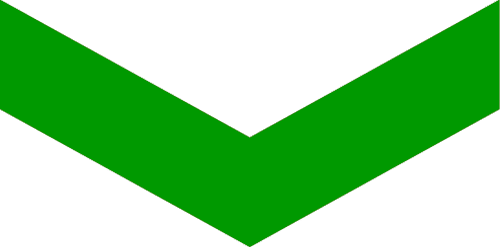
Fabrication de semelles orthopédiques en impression 3D
Impression 3D de semelles rigides avec la Fuse 1+ 30W et poudre Nylon 11 Faire appel à Cylaos-MédicalDécouvrir la solution FormlabsLa Podologie Traditionnelle : Entre Expertise et Limites
Une méthode longue et couteuse
Dans l’univers de la podologie, la création de semelles orthopédiques représente un équilibre délicat entre l’art et la science. Traditionnellement, les podologues se fient à leur savoir-faire pour modeler des semelles qui répondent aux besoins uniques de chaque patient, souvent à l’aide de moulages en plâtre ou de techniques de modélisation directe. Cette approche, bien qu’artisanale et personnalisée, présente des limites en termes de précision, de temps et d’efficacité.
Défis et Contraintes Actuelles
Malgré l’expertise des podologues, plusieurs défis persistent avec les méthodes conventionnelles. La précision reste sujette aux aléas du processus manuel, tandis que le temps consacré à la fabrication de chaque paire de semelles peut s’avérer considérable. De plus, la capacité de personnalisation, bien que centrale, est souvent entravée par les limites des matériaux et des techniques utilisées, posant un défi constant pour répondre aux besoins spécifiques de chaque patient.


La Révolution Fuse 1 : Au-delà de la Tradition

Une imprimante compacte et la moins couteuse du marché
La solution Fuse 1 de Formlabs marque un tournant dans le domaine de la podologie. Utilisant la technologie d’impression 3D SLS (Selective Laser Sintering), cette approche numérique permet de créer des semelles orthopédiques sur mesure avec une précision et une rapidité inégalées. Le processus commence par un scan 3D du pied, suivi d’une conception assistée par ordinateur (CAO) qui permet d’ajuster finement chaque détail de la semelle en fonction des besoins orthopédiques du patient. Cette méthode assure une personnalisation sans précédent, transformant la vision traditionnelle de la podologie.

Réduction des coûts
Avec le flux de travail, de nombreuses étapes sont désormais numériques et ne nécessitent pas de matériaux ou de main-d’œuvre importante. L’achat d’un scanner 3D et d’un logiciel de conception est moins coûteux que les grandes quantités de mousse et de produits chimiques liquides.
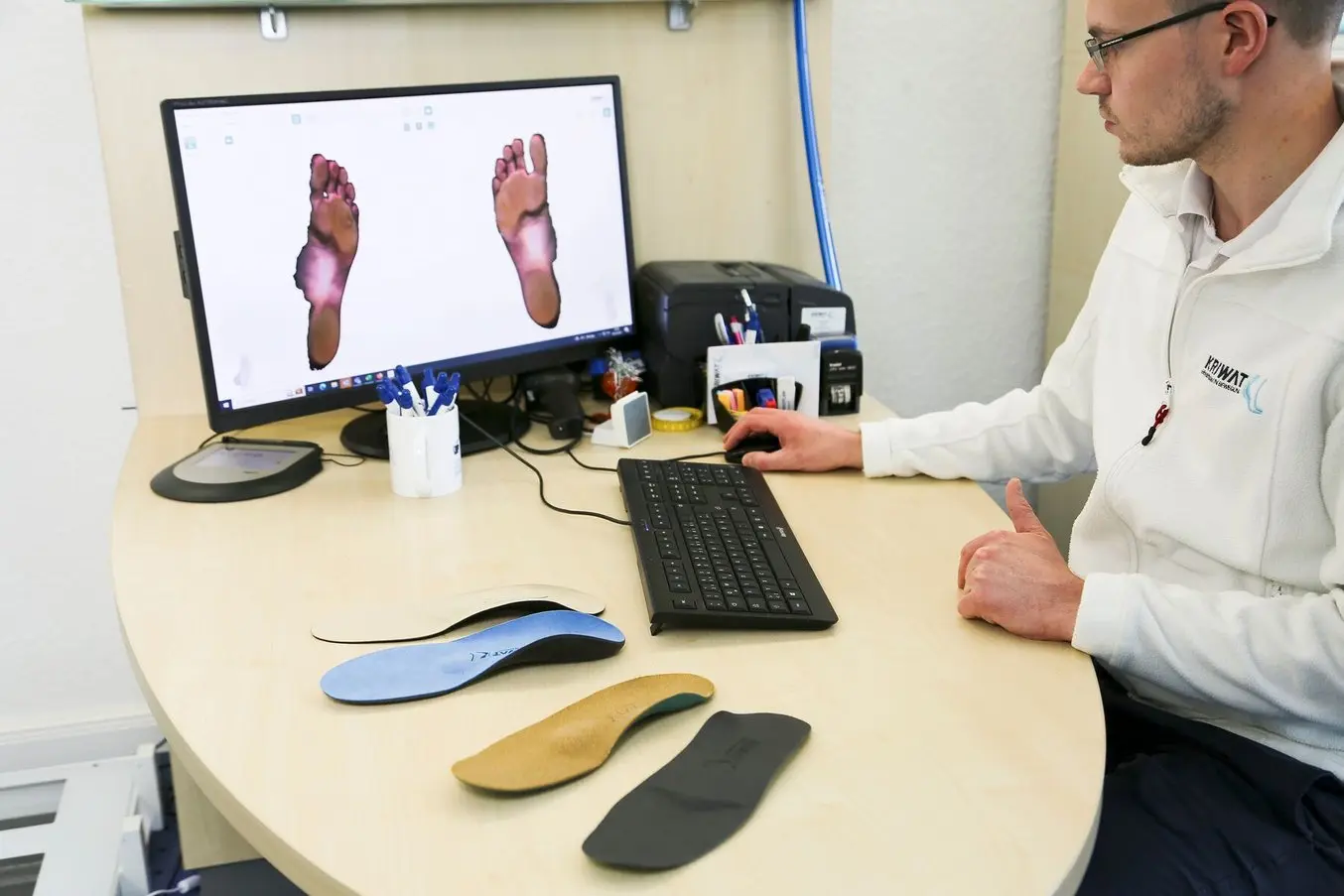
Processus de travail simplifié
Les pièces imprimées ne nécessitent pas de supports, peuvent être imprimées ensemble en une seule fois, et les pièces finies présentent une surface légèrement rugueuse, idéale pour le collage d’additifs et d’enveloppes pour les différents types de produits finis.
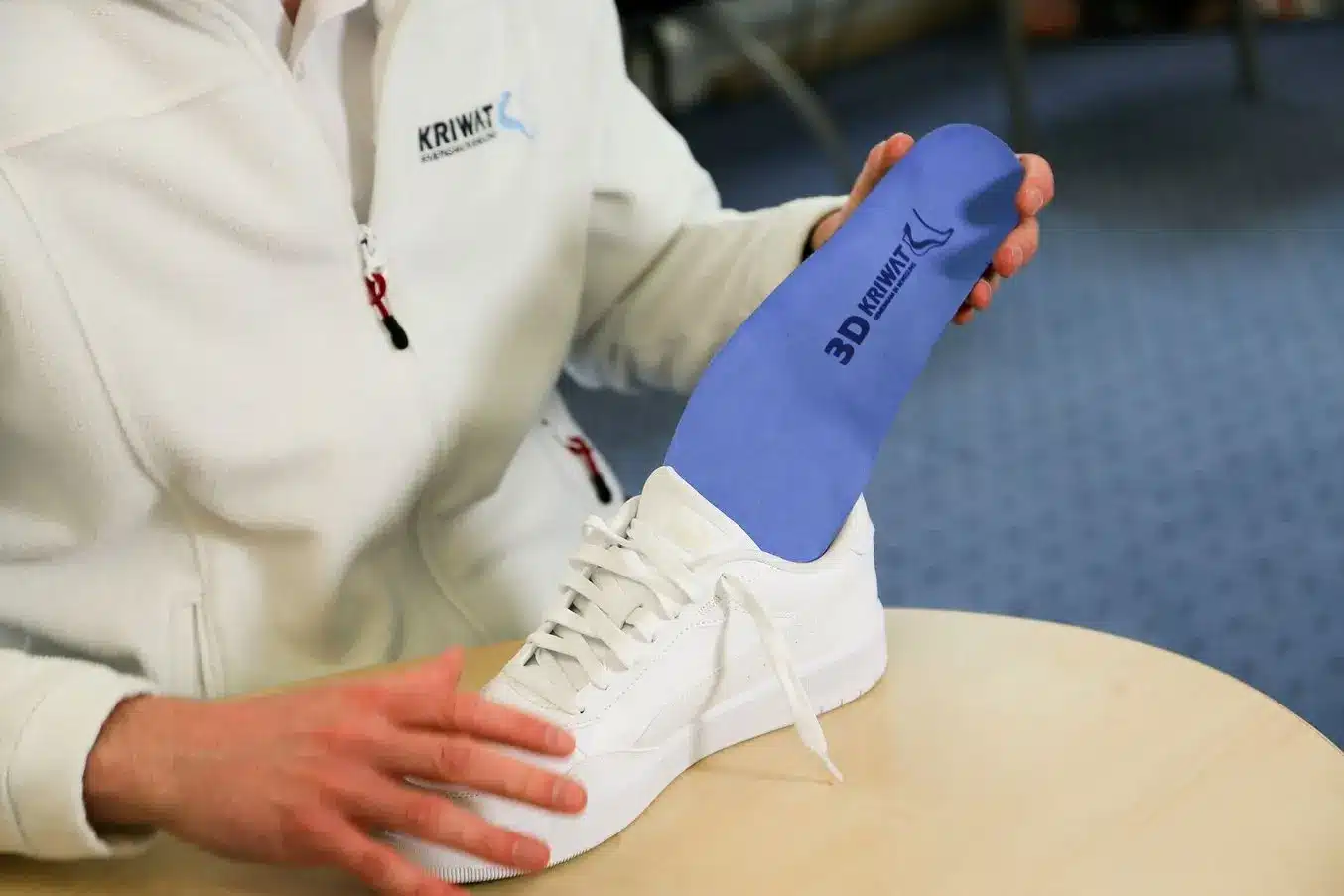
Gains de temps
Il est possible de réaliser un scan 3D, de créer un modèle numérique le même jour, de le grouper avec d’autres semelles et de toutes les imprimer avec la Fuse 1+ 30W pendant la nuit. Vous pouvez alors post-traiter les pièces, suivre le processus traditionnel de production et terminer les semelles le lendemain.
Cas d’application Kriwat : semelles orthopédiques
Découvrez comment Lais Kriwat, le fils du fondateur de Kriwat GmbH , a mis au point un flux de travail numérique pour la production de semelles grâce à l’impression 3D à frittage sélectif par laser (SLS) afin de moderniser l’entreprise et de relever ces défis. L’entreprise est ainsi sur la bonne voie pour produire 10 000 paires de semelles cette année grâce à l’impression 3D.
Guides : en savoir plus sur la solution

Impression 3D de semelles rigides avec la Fuse 1+ 30W et Nylon 11 Powder
Découvrez comment produire des semelles intérieures solides et ductiles dépassant les 4 millions de cycles de pliage grâce à l’écosystème SLS compact et abordable de Formlabs. Ce guide complet vous aidera à vous lancer dans la production d’enveloppes de semelles sur la Fuse 1+ 30W.
OBTENIR LE GUIDE |

Analyse des performances mécaniques de semelles rigides imprimées en 3D et fabriquées de manière traditionnelle
Cette étude compare les propriétés mécaniques associées à trois matériaux et méthodes de fabrication utilisés pour produire des enveloppes rigides personnalisées de semelles orthopédiques.
OBTENIR LE GUIDE |
Vous souhaitez faire une demande de benchmark ?
Contactez-nous par formulaire ou appelez au 02 30 96 36 84 Demande de benchmarkNous appelerDécouvrez les applications médicales
UPSA Stimule l’Innovation dans la Fabrication Pharmaceutique avec l’Impression 3D
"Nous avons utilisé l'impression 3D pour l'outillage de nouvelles pièces et de pièces de rechange, l'amélioration de la ligne de production et la création de pièces sur mesure et de prototypes...
H&T Presspart réduit ses couts d’outillages de plus de 50% avec Stratasys
Précision et qualité du moulage par injectionH&T Presspart, spécialiste des composants de haute précision pour l'industrie pharmaceutique, recherchait une solution d'impression 3D pour créer des...
Création d’un système avancé d’administration de médicaments par Syqe
Créer des dispositifs médicaux innovants qui résolvent des défis cliniques non résolus est toujours une tache formidable. Ajoutez a cela des contraintes de temps extrémes et la nécessité d’inventer...